DWoP - Drill the Well on Paper
DWoP - Drill the Well on Paper

HPHT Well Delivery
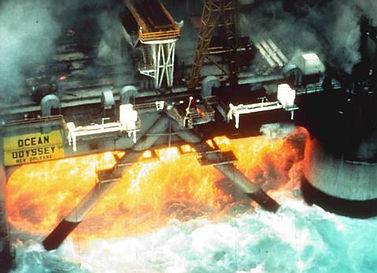
Event Type
Days
Aimed at
Workshop
5 days
This course is intended for personnel directly or indirectly involved in the delivery of HPHT wells. The following, in particular, would benefit from attending:
-
Office based planning and delivery Well Engineers
-
Drilling Superintendents
-
Wellsite Drilling Supervisors
-
Drilling Contractors:
-
Drillers, Tour Pushers, Toolpushers and Rig Superintendents
-
Rig Managers and OIMs
According to API Standard 53, HPHT (High Pressure - High Temperature) wells have a potential pressure greater than 15,000 psi (1,000 Bar) at the wellhead or a potential flowing temperature of greater than 350 °F (177 °C) at the wellhead. NORSOK DE-10 set’s the threshold for HPHT rather lower: a well with expected shut-in pressure exceeding 10,000 psi, (690 bar), and a static bottom hole temperature higher than 300 °F (150 °C).
Regardless of the definition you choose; these conditions are increasingly encountered in many basins worldwide, as exploration and production examine deeper and hotter objectives. Operating in these environments take drill crews, wellsite supervisors and Operator and Drilling Contractor management well beyond the scope of IWCF or IADC Wellcap Well Control Certification.
In attending this course, participants will gain knowledge and develops skills relating to HPHT Well Delivery. The course focuses on key characteristics of HPHT sections and the challenges of drilling them safely and efficiently. It covers a range of topics including:
-
Narrow Drilling Margins – Kick tolerance, Pore pressure prediction
-
Well Behaviour – the impact of both high pressures and temperatures, and significant changes in temperature on the observed behaviour of the well
-
Well barriers – the impact of temperature and pressure on primary and secondary well barriers
-
Operational Planning - Rig selection, BOP equipment performance, mud degasser capacity
-
Well Delivery - fingerprinting, well bore breathing, high-reliability drilling practices
-
Well Control – practical well control for on bottom, off bottom and out of hole well control, kicks and losses
Scenario Based Training - The course can be delivered as an in-house course for rig teams preparing for a critical well. Such in-house courses typically include the well modelled on a Drilling Systems Drilling Simulator with a number of scenarios modelled during the course. Such sessions facilitate the evaluation of command and control capabilities and the development of Crew Resource Management skills.
Competence Development
At the end of this course delegates should be able to:
-
Understand the differences in well design between HPHT and conventional wells
-
Explain and describe the challenges of well control in HPHT environments
-
Identify rig equipment critical to HPHT well delivery and select rigs suitable for HPHT drilling operations
-
Explain how MPD can assist in the safe drilling of HPHT wells
-
Evaluate the gas handling capacity of a poor-boy degasser and calculate potential gas loading rates during well control operations
-
Explain HPHT specific drilling practices including the use of a drilling stand
-
Explain how ballooning / wellbore breathing can be identified and managed
-
Describe what is meant by fingerprinting and develop rig procedures to use fingerprinting effectively
-
Describe how thermal effects compromise traditional kick detection techniques and how this can be mitigated
-
Manage tripping operations and reliably use trip sheets
-
Implement well control procedures to manage on-bottom, off-bottom and out of hole well control events and deal with plugged drillstring and loss of circulation
-
Describe the development and symptoms of formation breakdown during a kick leading to an underground blowout and the change in emphasis once this has occurred
-
Explain why crew training and communication are critical aspects in successful HPHT well delivery
Course Content
The following subjects will be addressed during the course:
Characteristics of HPHT wells –the industry definition of an HPHT well is reviewed the characteristics that make HPHT wells challenging are examined. The session looks at the origin of abnormal pressure and focuses on the narrow pressure margins between pore pressure and formation strength and its profound impact on kick tolerance in the region of the transition zone. Gas, Temperature and Compression Laws are discussed as is gas migration. A review of HPHT well control events focuses attention on the key differences between HPHT and conventional wells. Unique challenges including high pressure low permeability formations are addressed.
Well Barriers in HPHT wells – This section includes a review of the principals of casing design with a focus on the effects of temperature on casing design criteria, such as load and yield strength changes. The importance of casing wear and it’s impact on casing design and well integrity are discussed. Kick tolerance principals are reviewed along with methods to risk uncertainty.
Rig and equipment selection – A detailed review of the essential requirements of the rig and drilling equipment is provided which covers the rig, fluids control equipment and well control equipment, and instrumentation. Particular attention will be given to qualification and testing of BOP equipment and the sizing and performance assessment of surface gas handling equipment.
Managed Pressure Drilling (MPD) - MPD offers solutions to a number of the challenges of HPHT well delivery, specifically the narrow margin between pore and fracture pressure through the transition zone. Some Operators require all “dry BOP” HPHT wells to be drilled with MDP in place while recent riser developments are seeing subsea and deepwater HPHT wells using MPD equipment too. This section addresses the benefits of MPD operations and examines the equipment and practises for its implementation in HPHT wells.
HPHT Drilling Practises – High reliability well delivery requires the implementation of drilling practises that can mitigate problems associated with high mud gradients / mud rheology, narrow margin environments and thermal effects. Such practises must address pressure limitations of conventional mud circulation systems such that the well can be safely closed in with high surface pressures at any time. This section addresses HPHT processes and practises including the development steps of well specific HPHT drilling procedures. A process assurance mechanism - the “Safe Drilling Checklist” – is introduced. Trip management including tripping with core barrels is discussed as is the management of pump off events. The.
Fingerprinting –the impact of temperature in fluid density and volume downhole means that conventional well control signals are less reliable in HPHT operations. It is critical to understand the normal behaviour of a well such that abnormal behaviour can be rapidly identified and reacted to. Proactive information gathering or “fingerprinting” prior to and while drilling an HPHT section achieves this. The array of data to be analysed and modern mud logging techniques that can be used are addressed.
Primary Well Control – The prevention of kicks by maintaining adequate BHP to overbalance permeable formations is a fundamental goal when drilling any well. It is complicated in HPHT wells due to the effect of temperature changes on drilling fluid throughout the wellbore. The narrow margins between drilling fluid gradient and formation strength in HPHT wells also makes control of excessive wellbore pressures equally critical. The effect of temperature and pressure on drilling fluid density, the importance of ECD management, and use of PWD is explained. The importance of operational procedures to minimise surge and swab effects is emphasised. Kick tolerance and gas behaviour is discussed in terms of the effects of temperature and the importance of monitoring gas while drilling is explained. Ballooning, breathing and supercharging will be explained along with techniques to differentiate between these effects and loss of primary well control.
Secondary Well control – Comprehensive knowledge and sound skills in the principals and practises of well control are critical to HPHT operations. This section looks at common causes of kicks, kick detection challenges including gas solubility in oil based muds and early kick detection technology. The reliability of surface pressure readings and challenges of interpreting downhole conditions from them are highlighted. Well control procedures to combat influxes taken with the drillstring on bottom, off bottom and with the drillstring out of the hole are reviewed. These will include driller’s method, volumetric method, bullheading, combined volumetric and stripping method and snubbing. The challenges of hydrate formation and its mitigation is also addressed.
Tertiary Well Control – Conventional well control techniques require the wellbore pressures to remain below the formation breakdown pressure in the open hole. Where this is exceeded, less conventional steps need to be taken to recover primary well control. Given the narrow margin between formation pressure and fracture pressure in HPHT wells, the situation may arise where there are simultaneous influx and losses leading to underground flows. The causes and treatments for underground blowouts are described and explained.
Teamwork and Training – competence, teamwork and communications between well delivery team members is critical to ensure the safe drilling of HPHT wells. Clear definitions of roles and responsibilities are needed as is a good understanding of how all team members contribute to the delivery of the well. This section examines these roles and explores how rig team communication and performance on critical wells can be enhanced by processes such as “Drilling the Well on a Simulator”.
